In many types of systems, heat sources can't efficiently produce heat at the same time and rate as it's needed by the heat loads. Solar panels only produce hot water when the sun is shining. Wood boilers are much more efficient if they can run at full output, which will produce much more heat than is likely to be needed at that moment. Heat pumps can produce heat more efficiently when it's warmer outside, but that heat is needed when it's colder. Even oil and gas boilers are more efficient if they can run longer but less often.
Heat storage solves these problems by allowing the production of heat to be separated from the use of that heat. Water is almost exclusively used as a heat storage medium as it's safe, inexpensive, and outperforms all but the most exotic materials. Storage in almost all cases needs to maintain the maximum possible thermal stratification - that is, water that's as hot as possible at the top of storage, and water that's as cool as possible at the bottom. Ideally, there would be a sharp boundary (called a thermocline) between the hot and cool water. This configuration maximizes the effective energy storage capacity of any given volume of storage while supplying usefully hot water to the heat loads for the longest possible time.
There are many ways that storage can be integrated into a heating system. This tutorial will describe one of the simplest and most effective: use of storage as a hydraulic separator.
In this configuration, there are are two independent heat loops with the tank serving as part of both loops. The first loop takes cool water from the bottom of storage through a heat source (wood boiler, for instance) and returns it as hot water to the top of storage. This creates a layer of very hot water at the top of the tank which is pushed downwards.
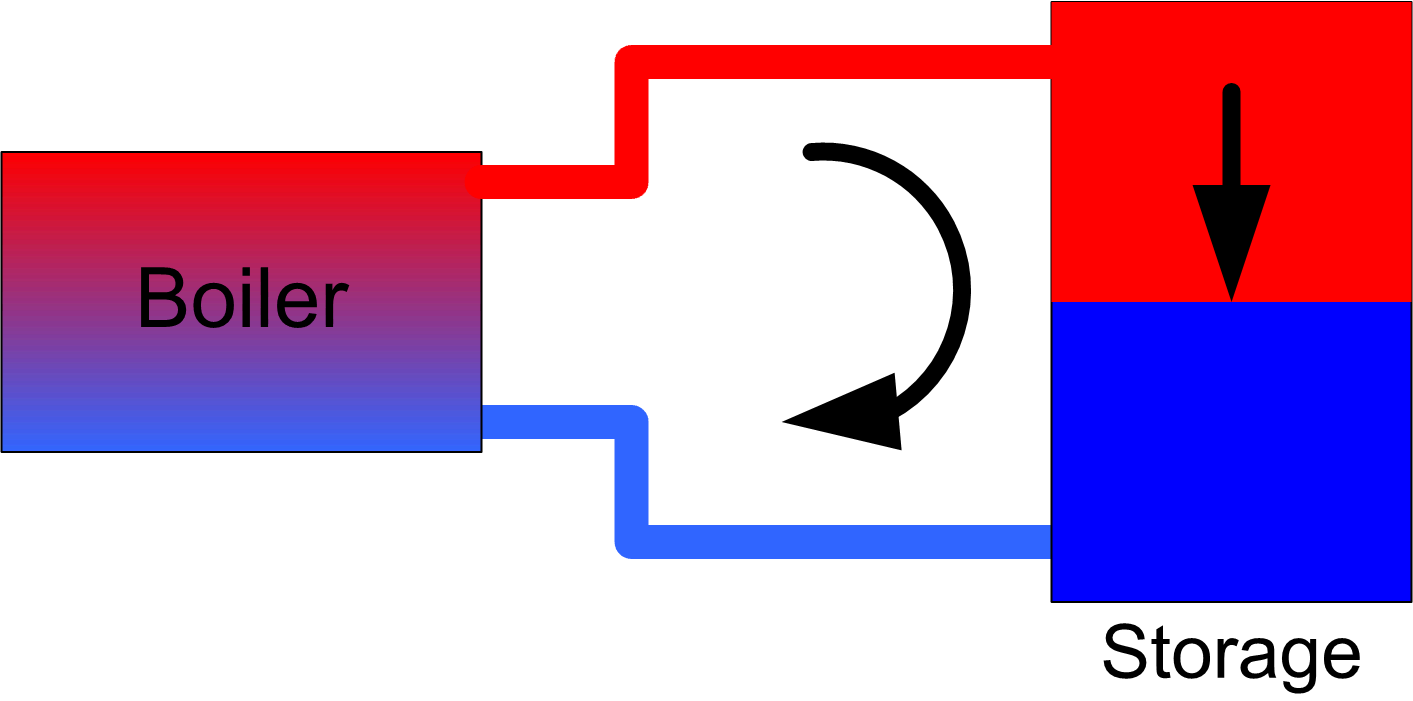
Figure 1: Boiler to Storage Loop
The second loop takes hot water from the top of storage, passes it through the heat load(s), and returns it as cool water to the bottom of the tank. This creates a layer of cool water in the bottom of storage that’s pushed upwards.
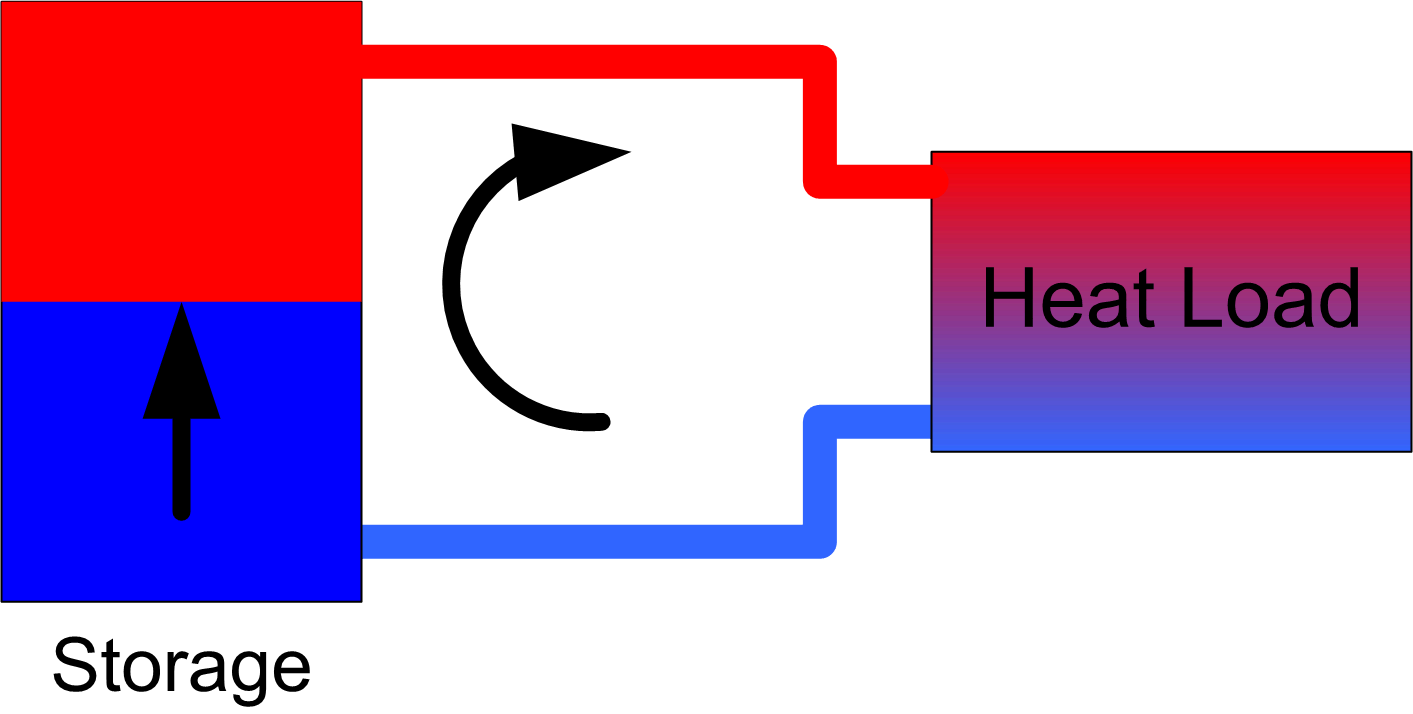
Figure 2: Storage to Heat Load(s) Loop
Of course, both of these loops can and often do operate at the same time. The beauty of this approach is that either loop can operate whenever it needs to, and each loop can operate at an optimal flow rate for current conditions.
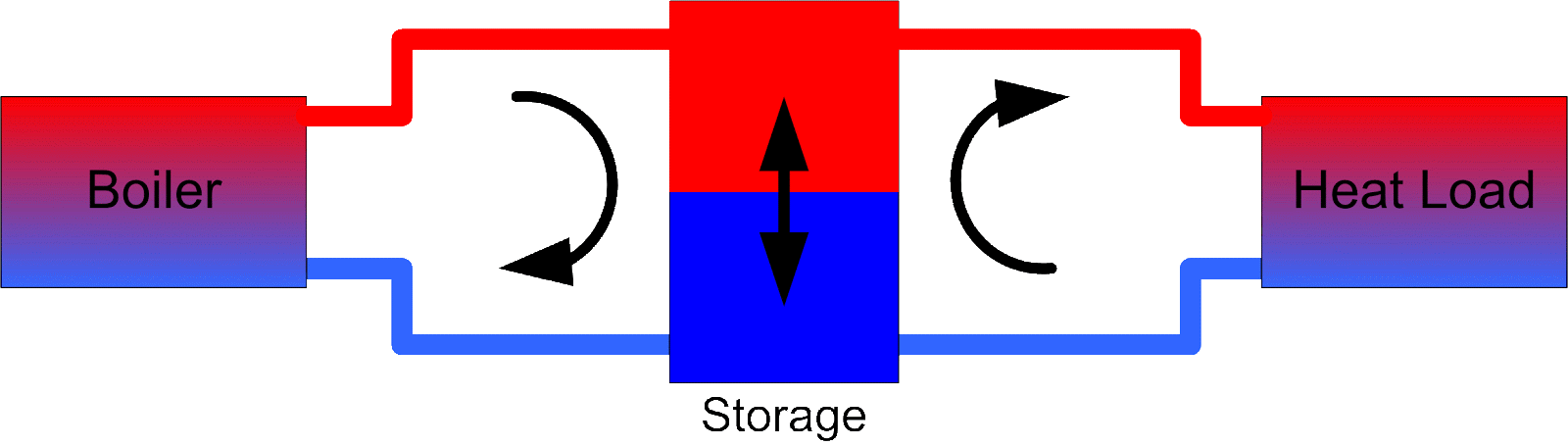
Figure 3: Combined Loops
If the heat source has a higher flow rate then the heat loads need, then the additional hot water goes into storage, pushing the hot/cold boundary downwards. If the heat loads need more flow than the heat sources are providing, then the hot/cold boundary moves upwards. All of this behavior happens automatically, irrespective of the number and types of heat sources and heat loads.
The inlets and outlets on the storage tank can be connected to a single port as shown here:
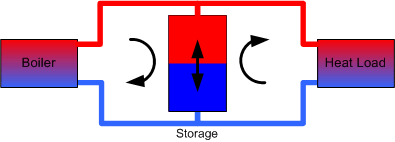
Figure 4: Combined Storage Port
While this is identical from a hydrostatic point of view, there are two potential problems. First, the path of lowest pressure drop across the tees is in a straight line. This creates the possibility of 'ghost flow' through the heat loads when the heat source is operating, and vice versa. Second, water is injected vertically into the tank. If the velocity is high enough, this can contribute to thermal mixing in the tank, decreasing stratification.
A better approach is to use side ports and bring incoming water through a tee oriented to not favor flow past the storage tank, as shown here:
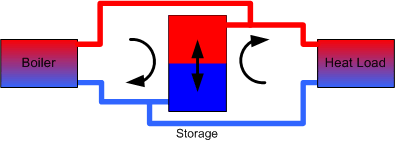
Figure 5: Side Ports and Ghost Flow reduction